What Is An Electronic Enclosure/Cage?
An electronic enclosure is an item used to protect a machine such as computer from damage. In addition, it protects you from electrical shock. The cage also protects the appliance from environmental elements such as dirt, chemicals, water, dust, or heat. Such things may affect how the machine works if you do not cover the machine well with a cage.
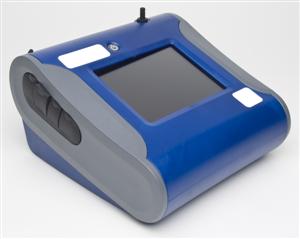
Source: Metromold
When you are using the computer or any other item, you often see the cage as the first thing. Therefore, it is important for the manufacturer to consider how the cage looks. Often, cages have holes that you can use to pass wires for connection to electricity.
People use plastics, steel, and other materials to make cages. Each of these items has its own pros and cons depending on where you use it.
Before buying a cage for any use, look at the pros and cons of each item that makes the cage. If you are not sure about the best item, look for an expert for help. You would rather use some more money for a skilled person, than having a bad enclosure for a long time. It is also necessary to check whether using such item is good for you or not. Like other items, plastic cages have advantages.
For more about plastic enclosures for electronics and instruments, continue reading this paper. You will learn more about benefits of plastic cages.
What are the Benefits of Electronic Instrument Plastic Enclosures or Plastic Cages?
You will come across plastic cages many times, if you are in a building. In fact, if you are in the office, the closest plastic electronic cage could be just 5 meters from you. For an office with internet and electronics, you will find plastic cages near you.
To know the advantages of plastic cages, imagine life without plastic cages. You may use cages for very expensive and dangerous appliance. If there were no cages, such appliance would bring all forms of dangers to people in the office or home. Fires and damage can cause loss of money. You can take care of your property and prevent damage by using simple plastic cages.

Source: Decomtech
When you look at cages in factories, you may think that items such as aluminum and steel are better than plastic. Even if this is true for some areas within the facility, new types of plastic emerge daily and present better qualities. Glass-filled plastic that is very stiff and durable is a good example of new type of plastic.
Even if you ignore the other advantages of plastics, you will find that plastics are also easier to use and repair. Looking at the characteristics of plastic as compared to other cage items is the best way to check the advantages of plastic cages.
First, plastic is popular because it does not conduct electricity as metals do. Thus, this makes it the best choice for places where using an appliance may cause one to get electrical shock.
People also prefer plastic cages for areas where they want to use lighter items. The reason for this is that plastic is lighter than metals. So it is better to use plastic where support for heavy electronic and instrument cages is not enough.
Plastics are cheaper than aluminum or any other item used for electronic cages. Plastics are also better if you consider all the work and cost it needs before it is ready for use. You will need more effort to make metallic cages look attractive.
As you choose the plastic cage, remember that there are two major types of plastics. The scientific names of these plastics are PC plastic and Phenolic plastic. Phenolic plastic is hard and lasts long. On the other hand, a PC plastic is strong and flexible, regardless of the temperature. Therefore, plastic type depends on how you are planning to use your appliance.
Conclusion
Plastic cages are growing in popularity with speed. More support for this idea is available in a study done by a company in 2011. The report says that the manufacture of plastics enclosures across the world will reach a worth of 10 billion pounds by the year 2017. It also predicts that in 2017, the world demand will have increased for both movable plastic cages and stationary plastic cages.
This report supports the idea that plastic brings many advantages for the people who use computers and similar items. Plastics solve the installation needs of most people because it is available in different types. When looking for appliance that uses enclosures, make a list of the needs from your item. If you fail to do that, you may choose a bad item that exposes the appliance or people to dangers.
Finally, you should ensure that you have all the necessary licenses from the government.